
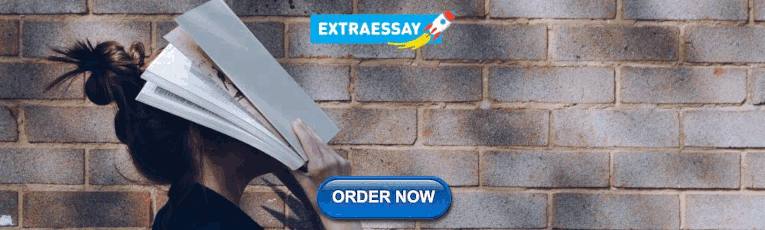
8-Steps to Solving Problems
- Published Aug. 19, 2009
- By Edward Constantine
- 354th Fighter Wing AFSO21 Process Manga

AFSO21 adopts 8-step problem solving model
- Published March 10, 2008
- By Maj. Jason Todd
- 14th Flying Training Wing Commander's Action Group

Senior Master Sgt. Spring Walden, 403rd Wing Inspector General Inspections superintendent conducts training for Self-Assessment Program managers April 3, 2022, at the 403rd Wing Headquarters, Keesler Air Force Base, Mississippi. SAPs and SAPMs are a critical aspect of the Air Force Inspection System and assist IGI in validating a unit's compliance in executing the four major graded areas of executing the mission, improving the unit, leading people and managing resources. (U.S. Air Force photo/Lt. Col. Marnee A.C. Losurdo)
Senior Master Sgt. Spring Walden, 403rd Wing Inspector General Inspections superintendent conducts training for Self-Assessment Program managers April 3, 2022, at the 403rd Wing Headquarters, Keesler Air Force Base, Mississippi. SAPs and SAPMs are a critical aspect of the Air Force Inspection System and assist IGI in validating a unit's compliance in executing the four major graded areas of executing the mission, improving the unit, leading people and managing resources. (U.S. Air Force photo by Lt. Col. Marnee A.C. Losurdo)
The 403rd Wing’s Self-Assessment Program managers are a crucial part of the Air Force Inspection System and assist the wing's Inspector General Inspections office in validating a unit’s compliance in executing the major graded areas of executing the mission, improving the unit, leading the people and managing resources. (Air Force graphic by Lt. Col. Marnee A.C. Losurdo)
Self-Assessment Program managers key to compliance
- Published April 12, 2022
- By Lt. Col. Marnee A. C. Losurdo
- 403rd Wing Public Affairs
Self-assessment is the evaluation of one’s actions or the processes used in accomplishing their job, and it’s something Senior Master Sgt. Spring Walden knows all about.
The Inspector General Inspections superintendent runs the Self-Assessment Program for the 403rd Wing, a key component of the Air Force Inspection System, referred to as AFIS.
According to Air Force Instruction 90-201, AFIS is designed to foster a culture of critical self-assessment and continuous improvement, providing a "photo album" versus a "snapshot" view of wing effectiveness. The Self-Assessment Program, better known as SAP, is how program managers such as Walden identify areas of non-compliance.
“I ensure overall quality and accuracy of the wing’s self-assessment program to provide the wing commander with trending analysis, areas of risk and needs for future funding and manning,” said Walden, who provides oversight and guidance to the wing’s 48 Self-Assessment Program managers, or SAPM, charged with running their unit’s SAP.
SAPMs such as Lt. Col. Natalie McKee, 403rd Aeromedical Staging Squadron, and Master Sgt. Katie Williams, 403rd Maintenance Group, track deficiencies and findings for their units and report to their commanders. They are a crucial part of the AFIS and assist IGI in validating a unit’s compliance in executing the major graded areas of executing the mission, improving the unit, leading the people and managing resources, said Walden.
McKee has been a SAPM since 2019 and Williams took on the additional duty in 2021.
“I am the eyes and ears for the commander on programs and compliance,” said Williams. “I monitor everybody’s checklist in MICT (Management Internal Controls Toolset), a tool we use to keep track of programs and compliance. If there are deficiencies, they have to come up with a corrective action plan and a root cause analysis. I’m monitoring the process for all those things, and if there is an area that we are not in compliance with, I help them in establishing a way forward in fixing the process and preventing it from happening again.”
SAPMs ensure self-assessment communicators, or SACs that are better known as checklists, are assessed and validated in MICT. They assist with effective program management and manage deficiencies by reviewing MICT for currency and effective correction action plans. In cases of non-compliance, continuous process improvement practices are used along with the Air Force’s 8-Step Practical Problem Solving Method to resolve the deficiencies.
“It’s a time consuming job,” said McKee, who spends time outside of the Unit Training Assembly reviewing MICT and informing unit personnel on changes in checklists and if they need to go back into MICT to provide better documentation.
“The answers to the questions in MICT need more than just a yes, no, or not applicable response,” said McKee. “Unless it involves classified information, it is best for the assessors and validators to paint a clear picture of how they are meeting the requirements of their AFI. It is important for them to describe their processes and to provide supporting documentation.”
Walden relies on SAPMs such as McKee and Williams to ensure MICT checklists are current and are assessed with detailed and accurate assessments to help ensure deficiencies are identified and corrected, which is key to providing effective communication between program managers and functional area managers at headquarters who monitor MICT regularly.
“A SAPM should have good communication skills, be well organized, with attention to detail,” said Walden.
In addition to having these attributes and running effective programs, according to Walden, McKee and Williams said training is important too. They both provide training to their Unit Self-Assessment Program Managers and unit members on how to use MICT and properly assess and validate their SAC checklists.
SAPMs, such as McKee and Williams, are a key part of the Commander’s Inspection Program, the wing commander’s interpretation of AFIS. It’s through the CCIP that leadership is able to determine the accuracy of self-assessment programs in the 403rd Wing.
“It’s vital that the wing embrace a culture of self-assessment and AFIS,” said Walden. “It takes everyone from commanders to Airmen to take an honest look at our programs, critically self-assess and identify those areas that need work and come up with ways on how we can do things better. It takes more than saying, ‘we are the Wing of Choice and we do our mission well,’ we have to prove it.”
Official websites use .mil
Secure .mil websites use HTTPS

An Air Force Smart Operations for the 21st Century, or AFSO21, event was held for Air Education and Training Command chaplains, Jan. 13, 2015, to help establish means for improving chaplain engagement with Airmen. AFSO21 is a mindset that focuses on eliminating waste and continually improving processes at the grassroots level. For some, AFSO21 gives Airmen tools at their level to make a difference and move the Air Force into a better direction. (U.S. Air Force photo by 1st Lt. Jose R. Davis)
Air Force Smart Operations for the 21st Century, or AFSO21, is dependent on an eight-step problem solving model, which is a combination of four process improvement efforts borrowed from proven business standard practices. AFSO21 is a mindset that focuses on eliminating waste and continually improving processes at the grassroots level. For some, AFSO21 gives Airmen tools at their level to make a difference and move the Air Force into a better direction. (Courtesy graphic)
To move a mountain, one must first begin by carrying away its small stones. In the same sense, Air Force Smart Operations for the 21st Century, or AFSO21, is a mindset that focuses on eliminating waste and continually improving processes at the grassroots level. For some, AFSO21 gives Airmen tools at their level to make a difference and move the Air Force into a better direction. (U.S. Air Force graphic by 1st Lt. Jose R. Davis)
- Published Feb. 19, 2015
- By 1st Lt. Jose R. Davis
- Air Education and Training Command Public Affairs

8-Steps to Bright Ideas
Airmen complete a hands-on scenario during an Air Force Smart Operations for the 21st Century course, titled “The 8-Step Problem Solving Method” at RAF Lakenheath, England, June 9. Nine courses have been held since August 2009 and are held monthly to train Airmen on a proper way to tackle difficult problems. (Pictured clockwise from top) Tech. Sgt. Kenneth Moncrief, 48th Communications Squadron assistant NCO in charge of airfield systems; Staff Sgt. Gregory Greer, 48th Aircraft Maintenance Squadron crew chief; Senior Master Sgt. Jeremy Krumenauer, 48th Force Support Squadron superintendent of manpower and organization; Airman 1st Class Chelsea Nobles, 48th Operations Group intelligence analyst; Staff Sgt. Alejandro Soto, 48th Logistics Readiness Squadron quality assurance technician; and Tech. Sgt. Brian Thomas, 48th Comptroller Squadron NCO in charge of customer support. (U.S. Air Force photo/Tech. Sgt. Nathan Gallahan)
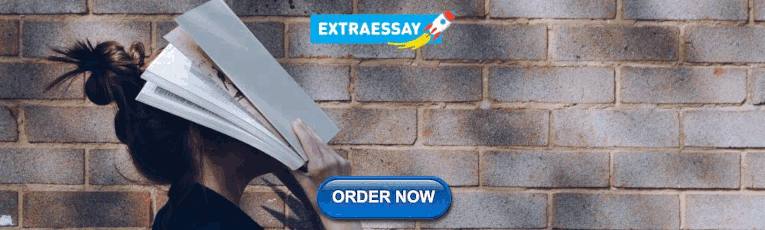
8-Steps of Bright Ideas
- Published June 11, 2010
- By Tech. Sgt. Nathan Gallahan
- 48th Fighter Wing Public Affairs
Official websites use .mil
Secure .mil websites use HTTPS

Air Force Smart Operations for the 21st Century, or "AFSO 21," is a program developed to identify waste and inefficiencies within the service, resulting in a more optimized, streamlined and efficient operations. In Air Mobility Command, the AMC AFSO 21 Office is applying an eight-step process in improving efficiency.(U.S. Air Force Graphic/Senior Airmen Heather Stanton and Jason Burton)
AFSO21 logo
AFSO 21: AMC office seeks to solve problems in eight steps
- Published Sept. 29, 2009
- By By Laura McAndrews
- Air Mobility Command Public Affairs

The Air Force Smart Operations for the 21st Century program was developed to help Airmen identify inefficiencies in business processes to minimize waste and provide continuous process improvement.
AFSO21: If it ain't broke, fix it anyway
- Published Jan. 24, 2012
- By Raquel Sanchez
- 1st Special Operations Wing Public Affairs

Eight step problem solving model for deficiency resolution
- Published Sept. 8, 2011
- By Ed Delker
- Office of the Inspector General OO-ALC gatekeeper
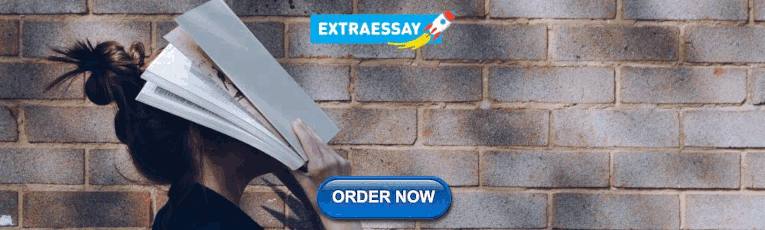
IMAGES
COMMENTS
EIELSON AIR FORCE BASE, Alaska -- The Air Force has embarked on a journey to eliminate problems from recurring using the Air Force Smart Operations for the 21st Century program. The Secretary of the Air Force and Chief of Staff of the Air Force both endorsed the 8-Step Problem Solving Model as the wave of the future for the Air Force in their June 2009 Joint memo.
Develop Countermeasures O O D A. a. Develop potential countermeasures. - Tools and philosophies from Lean, TOC, 6 Sigma and BPR as appropriate. b. Select the most practical and effective countermeasures. c. Build consensus with others by involving all stakeholders appropriately. - Communicate, communicate, communicate.
Air Force Smart Operations for the 21st Century, or AFSO21, has adopted a new 8-Step Problem Solving Model to achieve continuous process improvement. This model is based on the OODA Loop and will make it easier for Air Force members to eliminate waste in, ... The 8-step process is better than the current methods of Value Stream Mapping or Rapid ...
The Air Force 8-step problem solving model is taught to Airmen through AFSO21 and Professional Military Education programs to generate efficiencies and improve combat capabilities across the Air Force. Although the application was developed with a focus on AFSO21 facilitators, any Airman will benefit from the application's user-friendly steps ...
2.3 CPI IS PROBLEM SOLVING At the core of process improvement is solving problems that create waste in the day-to-day work of our Airmen. Waste and inefficiencies come in many forms and a significant amount of waste is a product of the processes and methods used. Many of these methods were never engineered in the first place. Instead
Scott AFB will be holding in-depth training in the eight-step process for non-commissioned officers and up on Oct. 19 to 20 and Nov. 16 to 17. For details call (618) 229-2233 or e-mail [email protected]. In life, it can take as many as eight steps to solve a problem. However, according to the Air Force's Smart Operations for the 21st Century ...
Air Force Problem Solving Process OODA - Observe, Orient, Decide, & Act 8-Step Problem Solving Model Team Members: Facilitators: Lt Col Matthew Cox, ACC/A4; Mr. Jeff Combs, ACC/A4; SMSgt Anthony Tomczak, 116 MXG/QA; MSgt John Ace, ACC/A4Y; Team Leader: MSgt Ken Hathaway (116 MXS/ISO) -and 27 other team members from 116 MXG 4.
8 steps. Airmen complete a hands-on scenario during an Air Force Smart Operations for the 21st Century course, titled "The 8-Step Problem Solving Method" June 9, 2010, at Royal Air Force Lakenheath, England. Nine courses have been held since August 2009 and are held monthly to train Airmen on a proper way to tackle difficult problems.
To assist leaders with the development and implementation of a strategic-level continuous process improvement approach, the course reviewed process improvement methodologies such as Lean, Six Sigma, Theory of Constraints, Business Process Re-engineering, Value Stream Mapping, and the Air Force CPI 8-Step Practical Problem Solving Model.
In cases of non-compliance, continuous process improvement practices are used along with the Air Force's 8-Step Practical Problem Solving Method to resolve the deficiencies. "It's a time consuming job," said McKee, who spends time outside of the Unit Training Assembly reviewing MICT and informing unit personnel on changes in checklists ...
8 -Step Problem Solving Process Team Members: 4. Determine Root Cause O O D A 1. Clarify & Validate the Problem O O D A 2. Break Down the Problem/Identify Performance Gaps 3. Set Improvement Target 6. See Countermeasures Through O O D A 5. Develop Countermeasures O O D A 7. Confirm Results & Process 8. Standardize Successful Processes
Air Force Smart Operations for the 21st Century, or AFSO21, is dependent on an eight-step problem solving model, which is a combination of four process improvement efforts borrowed from proven business standard practices. AFSO21 is a mindset that focuses on eliminating waste and continually improving processes at the grassroots level.
SCOTT AIR FORCE BASE, Ill. -- The Air Force Smart Operations for the 21st Century's 8-Step Problem Solving Model is being taught at Scott AFB to improve processes and increase efficiencies. This model is based on the OODA Loop (Observe, Orient, Decide, Act) that originated in the 1950s with Col. John Boyd, and is designed to make it easier for Air Force members to eliminate waste and improve ...
The first item of business for any team tackling a challenge using the 8-step problem-solving model is to clarify and validate the problem. This step must include the buy-in of every team member. If the team can't agree on a definition of the problem, the hope for an effective solution is nil. Secondly, they have to break down the problem.
8-Steps of Bright Ideas. Airmen complete a hands-on scenario during an Air Force Smart Operations for the 21st Century course, titled "The 8-Step Problem Solving Method" at RAF Lakenheath, England, June 9. Nine courses have been held since August 2009 and are held monthly to train Airmen on a proper way to tackle difficult problems.
The Eight-Step Problem Solving Process is a method for solving day to day issues as well as larger problems. Because of the benefits from using the process, the Air Force Inspector General has implemented and mandated the use of the "Eight-Step Problem Solving Process" to get to the root cause of all problems and employ long lasting corrective ...
For more information about the 1st SOW AFSO21 program or to submit a process improvement suggestion, contact Underwood at 884-7466 or [email protected]. Note: The base offers an 8-Step Problem-Solving workshop designed to assist airmen with organizational problem solving and decision making. This 2-day workshop is taught once a ...
Prepare NCO's to continue strengthening the Air Force culture, lead and manage teams, ... Problem Solving Overview 8 Problem Solving Overview 2 Types of Thinking 2 Types of Thinking 2 ... process. A comprehensive assessment measures the degree to which the educational needs (identified during the needs analysis) were met as a result of ...
utilizing the Air Force 8-Step Practical Problem Solving Model to refine problem statements, perform formal root cause analyses, and develop updated action plans and performance measures for each finding via a data-centric review. This process was facilitated by a third party to ensure
Eight step problem solving model for deficiency resolution. Published May 26, 2011. By Ed Delker. Office of the Inspector General. HILL AIR FORCE BASE, Utah -- In the last article we looked at problem solving for the first three steps of the process. Now we will look at Steps 4 and 5, but first here are some key things to keep in mind.
HILL AIR FORCE BASE, Utah -- This is part three in a series of articles from Hill Air Force Base Inspector General office on the problem solving model. In the previous articles we looked at problems solving for the first five steps of the process. Now we will look at the remaining steps, but first here are some key things to keep in mind.
first six steps in the 8-Step Problem-Solving Process. Did not explain how their input had a direct impact on at least two of the first six steps in the 8-Step Problem-Solving Process. Score Lessons learned from RIE Explained how they will apply at least (1) process improvement tool (e.g. SIPOC, SWOT, KPI development, etc.) to help their
"The eight-step process is a more disciplined, In life, it can take as many as eight steps to solve a problem. However, according to the Air Force's Smart Operations for the 21st Century program, eight steps to solve any problem is all it should. An official website of the United States government